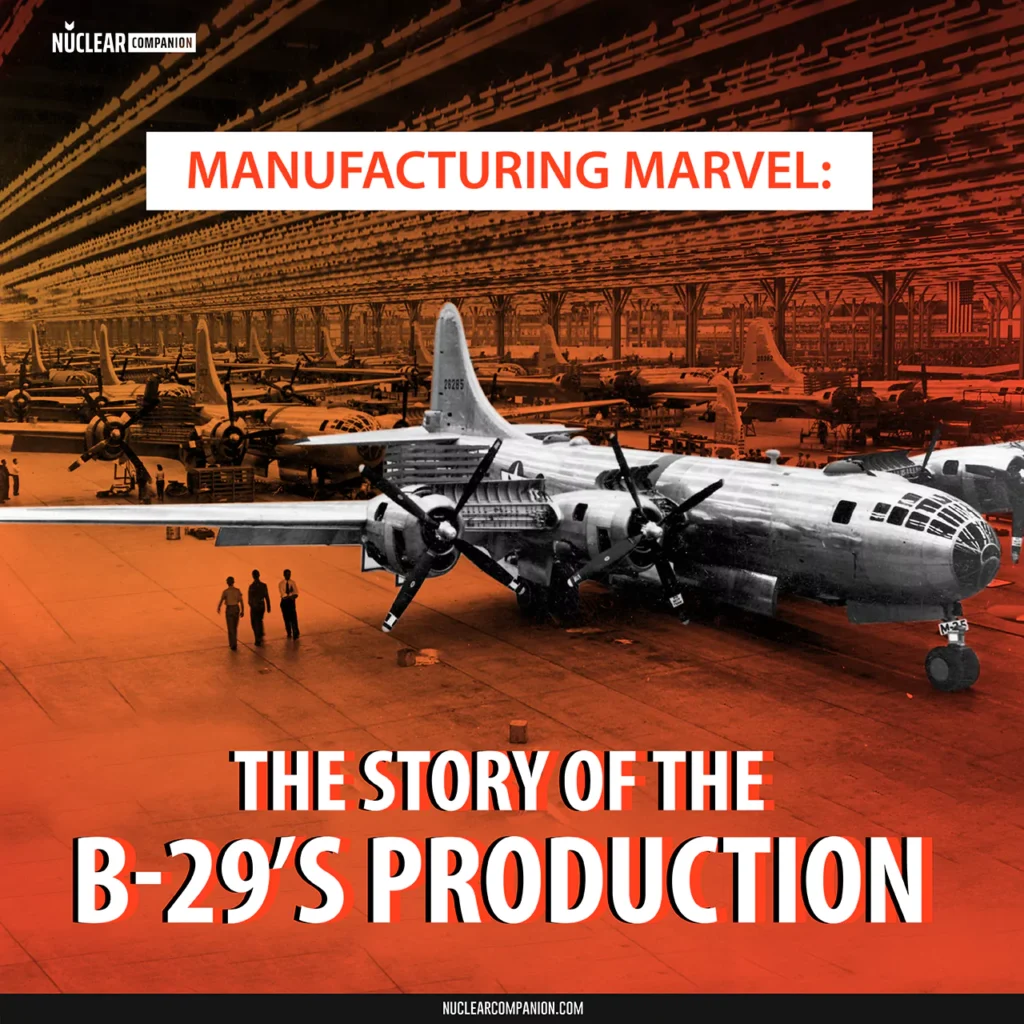
If the Manhattan Project was the biggest industrial program in U.S. history, producing the B-29 was the second biggest.
The first B-29 flew in September 1942, and by January 1944, the 100th aircraft had been accepted into service. Production of the B-29 rapidly increased throughout the year, with the 500th aircraft being accepted in July and the 1,000th in November. By March 1945, the 2,000th B-29 was accepted, and by June, the 3,000th. The peak production rate was reached in April with 300 aircraft per month, which further increased to 375 aircraft in the last full month of production.
This B-29’s production history was unparalleled during the war, and no other aircraft built after December 1941 was built in larger numbers or saw as much service as the B-29 in WWII.
Let’s dive into how the U.S. was able to do it!
Dividing the production
By the time of the first flight of the XB-29 prototype in September 1942, there were 1,664 Superfortress on the order book.
The first problem was that Boeing’s plants were overwhelmed in building the Boeing B-17 Flying Fortress and the demand for B-29s was so high that Boeing alone could not handle the large number of orders.
For the government, the only option appeared to be for Boeing and its subcontractors to establish new production facilities to construct the B-29 airframes, which required training an entirely new workforce. Meanwhile, other aircraft companies and their subcontractors were tasked with producing the components and equipment required for final assembly.
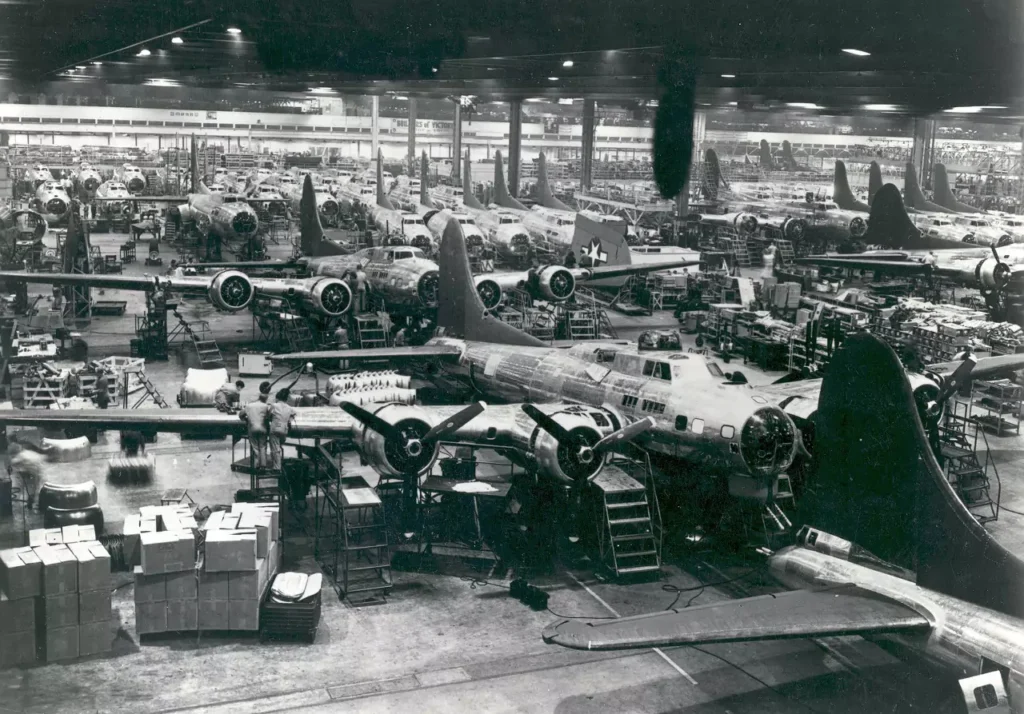
Originally, the government decided to divide the contract among four companies at newly built aircraft assembly plants:
- Boeing at Plant #2 in Wichita, KS. This plant was producing B-17s and would be enlarged.
- North American Aviation (a part of General Motors) at Aircraft Assembly Plant No 2, Kansas City, KS.
- Bell Aircraft Corp. at Aircraft Assembly Plant No 6, Marietta, GA.
- Fisher Body Division of General Motors at Aircraft Assembly Plant No 7, Cleveland, OH.
But it didn’t last long.
With an eye on post-WWII airplane production, Boeing considered North American a potential commercial threat and removed them from the B-29 contract. Instead, North American was asked to focus on manufacturing its B-25 bomber at the Kansas City plant
In August 1942, a deal was struck between Boeing and the US Navy where the Navy would relinquish control of Boeing’s plant in Renton, WA in exchange for a share of the B-25 production in Kansas City. This deal allowed Boeing to convert the Renton plant for B-29 production, but it also led to legal disputes.
Additionally, in July 1943, the B-29 contract with the Fisher Body Division of GM was transferred to the Glenn Martin Co., allowing Fisher to focus on the development and production of the XP-75 ‘Eagle’ fighter.
Finally, the companies and plants to fully assemble the B-29 were:
- Boeing at their Plant 2 in Wichita, KS
- Boeing at their plant in Renton, WA
- Bell Aircraft Corp. at Aircraft Assembly Plant No 6 at Marietta, GA
- Glenn L. Martin Co. at Aircraft Assembly Plant No. 1 at Fort Crook (Omaha), N
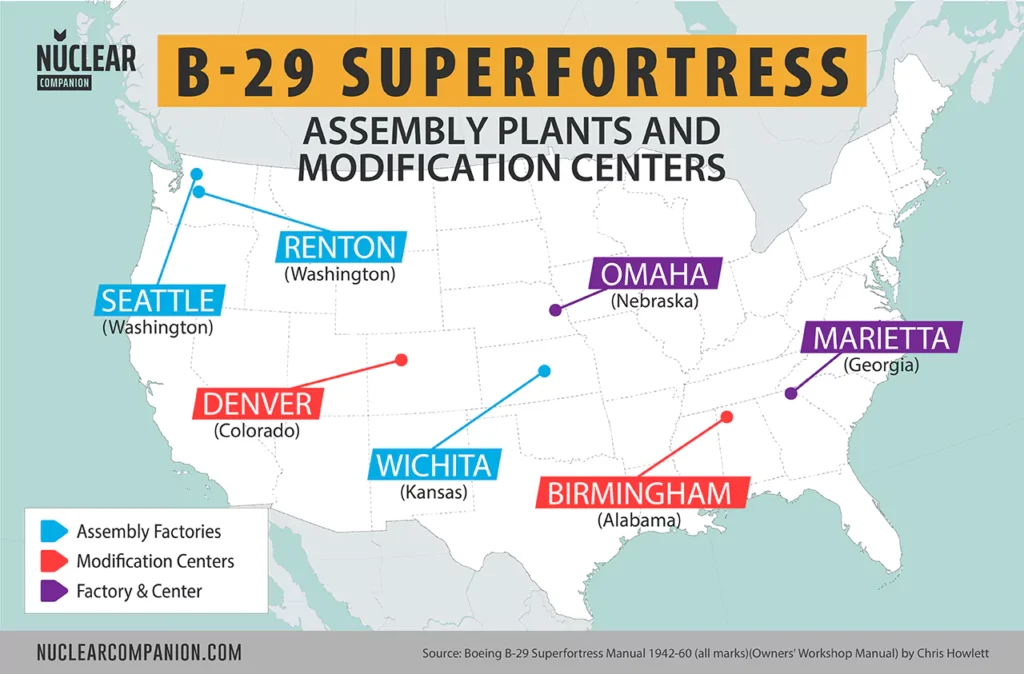
The multi-line Assembly system
The second problem was that building the B-29 was not the same as building a B-17. The B-29 was an imposing aircraft, with a size twice the weight of a B-17. Its mechanical and electrical systems were highly intricate, making it the most challenging aircraft to construct during World War II.
Engineers and managers at Boeing realized that the assembly-line design used at Willow Run by Ford could not handle the size and complexity of the B-29 Superfortress, with its 40,540 different parts and 600,000 rivets.
Interesting Fact
One B-29 required 12 tonnes (27,000 lb) of aluminum sheeting, over 450 kg (1,000 lb) of copper, 600,000 rivets, approximately 14 km (9 miles) of wiring, and 3 km (2 miles) of tubing for its construction.
To solve this, Boeing came up with a solution called “multi-lining” developed by production engineer Oliver West, which replaced the traditional single assembly line with six lines that converged around three final assembly lines at the entrance of the plant. Workers on each line were assigned specific sections of the B-29, with pushcarts, forklifts, and conveyors transporting parts to each line.
The sections were kept as small as possible until final assembly when cranes placed them into the final assembly bay, where four B-29s were assembled at once. Workers then added wings, electrical wiring and control systems, propellers, and landing gear.
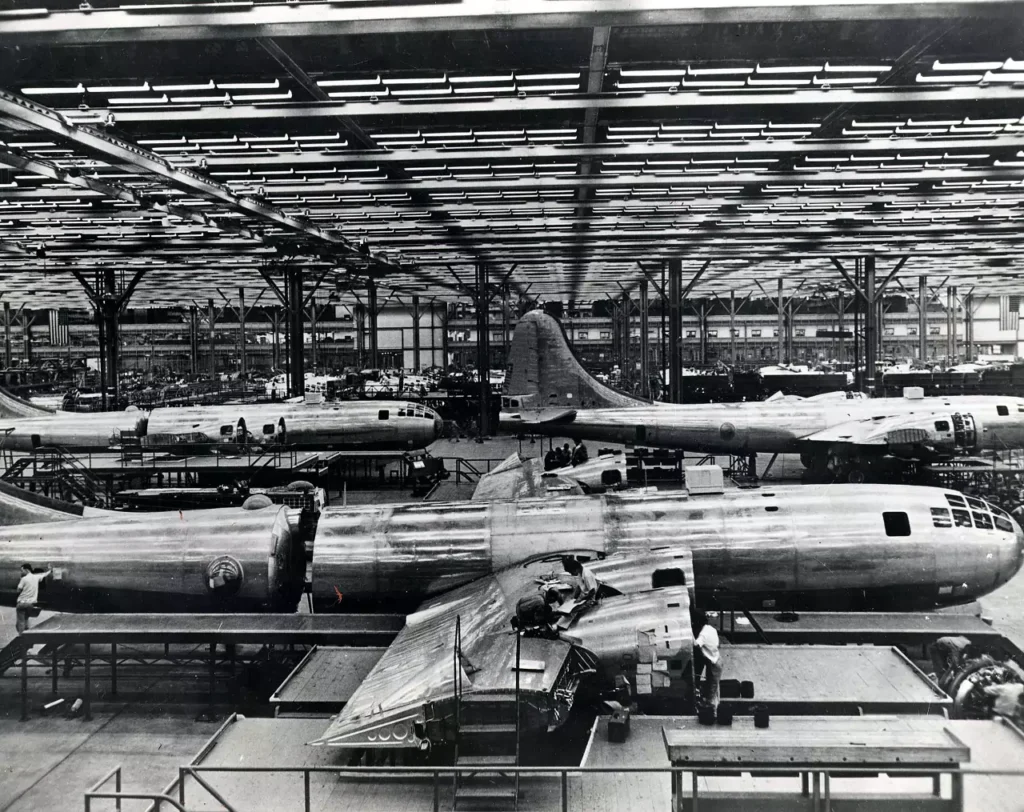
This multi-assembly-line method was a revolution in American manufacturing and became standard at all B-29 plants, saving time, man-hours, and costs compared to Willow Run, as it required fewer workstations and allowed for the almost seamless introduction of engineering modifications.
Boeing operated four lines, Bell’s plant in Marrietta used two parallel lines and Martin’s Ohama plant, being the smallest one, operated only one.
The B-29 factories
As mentioned before, four key production facilities located in four cities across the country were involved in the monumental effort. Wichita, Marietta, Renton, and Omaha were the centers of this ambitious project, each tasked with producing B-29s for Boeing in staggering quantities. These plants would go on to employ tens of thousands of men and women, playing a crucial role in transforming the local economies.
Let’s get into them:
Boeing-Wichita
In October 1940, the groundbreaking ceremony for the construction of the Boeing Wichita Plant was held. Upon completion, the plant spanned over 185 acres, encompassing 2.8 million square feet, and costing $26 million to build.
The main assembly floor of Plant #2 measured 1.7 million square feet, with two primary assembly lines stretching 750 feet in length, topped with a 300-foot roof equipped with built-in windows to allow for natural light.
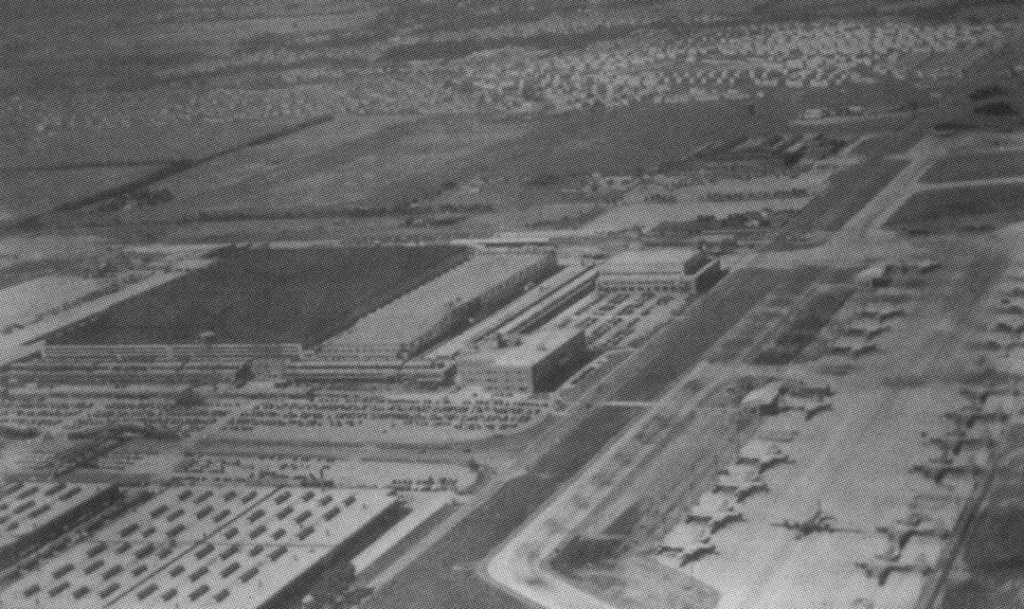
Assembly of B-17 parts commenced immediately after the plant was completed, with parts being shipped to Seattle and Los Angeles. However, in September 1941, a $215 million contract was awarded to Boeing to produce 250 B-29 bombers.
At its peak, the plant employed 15,000 workers in two shifts. In total, the Boeing Wichita Plant produced 1,769 B-29 aircraft, accounting for 44% of the entire B-29 production.
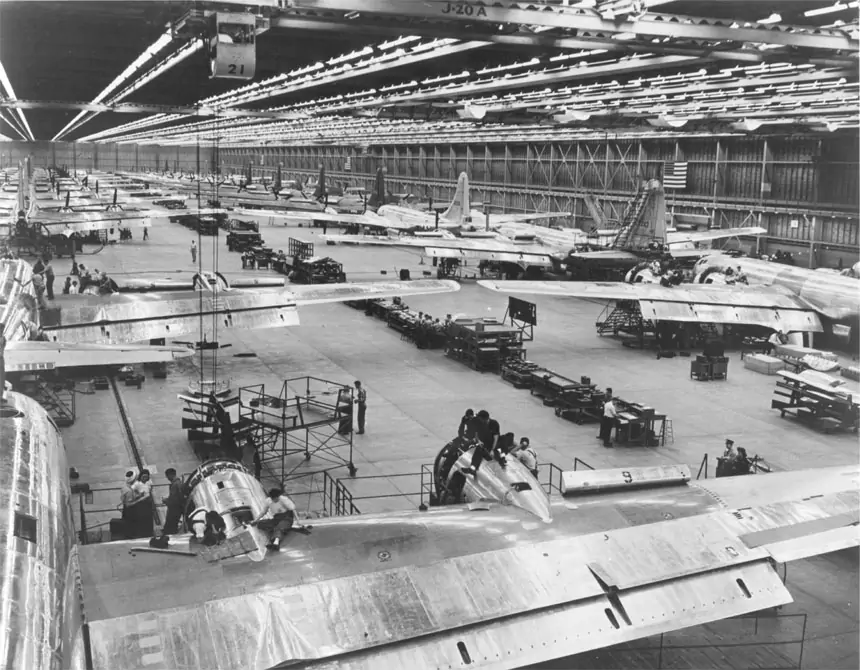
The first B-29-BW aircraft, designated as B-29-1-BW (42-6205), was accepted by the USAAF on March 3, 1944. The last Wichita-built Superfortress, a B-29-100-BW (45-21872), was manufactured on September 26, 1944, and delivered to the USAAF on October 10, 1944.
Bell-Atlanta (Marietta)
Located in Marietta, Georgia, about 20 miles northwest of Atlanta, the plant covered an enormous 3.96 million square feet, making it the largest dedicated to B-29 production. However, despite its size and potential, the Bell-Atlanta Plant faced numerous challenges that hindered its production output.
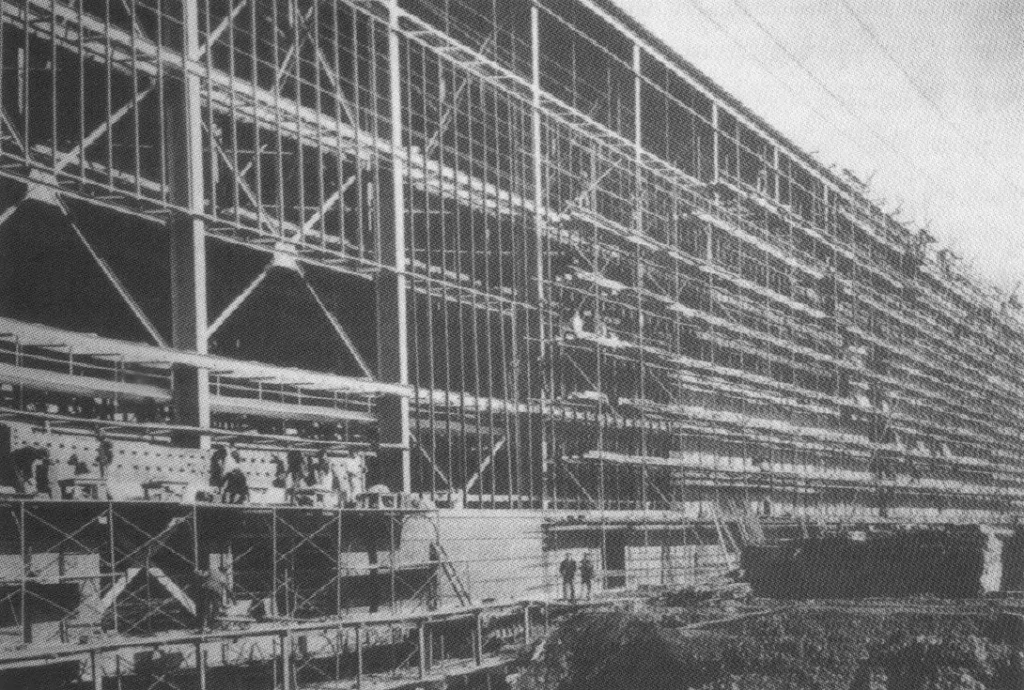
Construction of the plant took place from 1942 to 1943, with an investment of $47 million in taxpayer dollars towards the plant, its equipment, and adjacent runways. The plant occupied more than twice the area of the Renton or Wichita plants, yet it experienced problems from the start, including an inadequate workforce. Despite these challenges, the Bell-Atlanta Plant eventually started producing B-29s and B-29Bs, but the journey was far from smooth.
The shortage of materials and Bell’s relative lack of experience building large aircraft combined with poor communication between Bell and Boeing made it difficult for the plant to get off the ground.
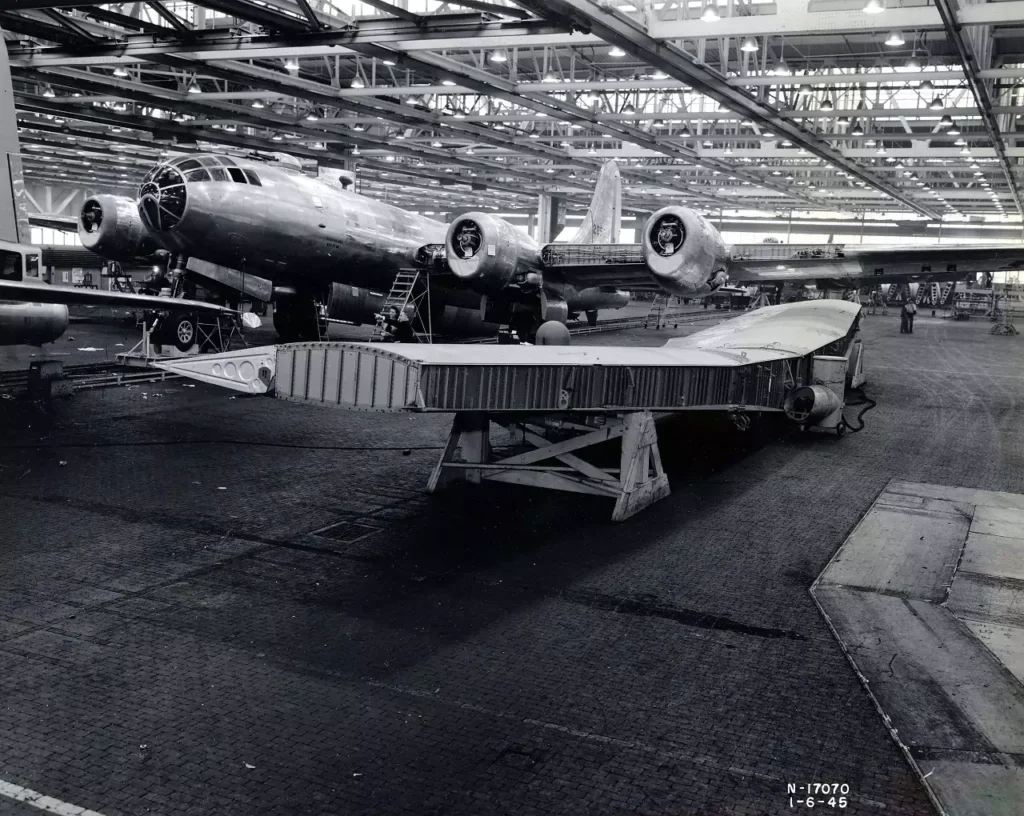
By the end of 1944, 17,200 workers were employed at Plant #6, working two nine-hour shifts, seven days a week. The labor force peaked at 27,000 in the spring of 1945.
By the end of the war, 668 Superfortresses had left the Marietta plant, a far cry from the 1,200 originally ordered.
Martin-Omaha
The Martin Omaha facility was established in 1941 to assemble the B-26 Marauder medium bomber for $20 million. The construction was carried out by the Army Corps of Engineers, including Assembly Plant #1 and Plant D, which had a total area of 1.2 million square feet and cost $10 million.
In April 1943, the Air Force decided to discontinue the B-26 production and instead focus on producing the B-29.
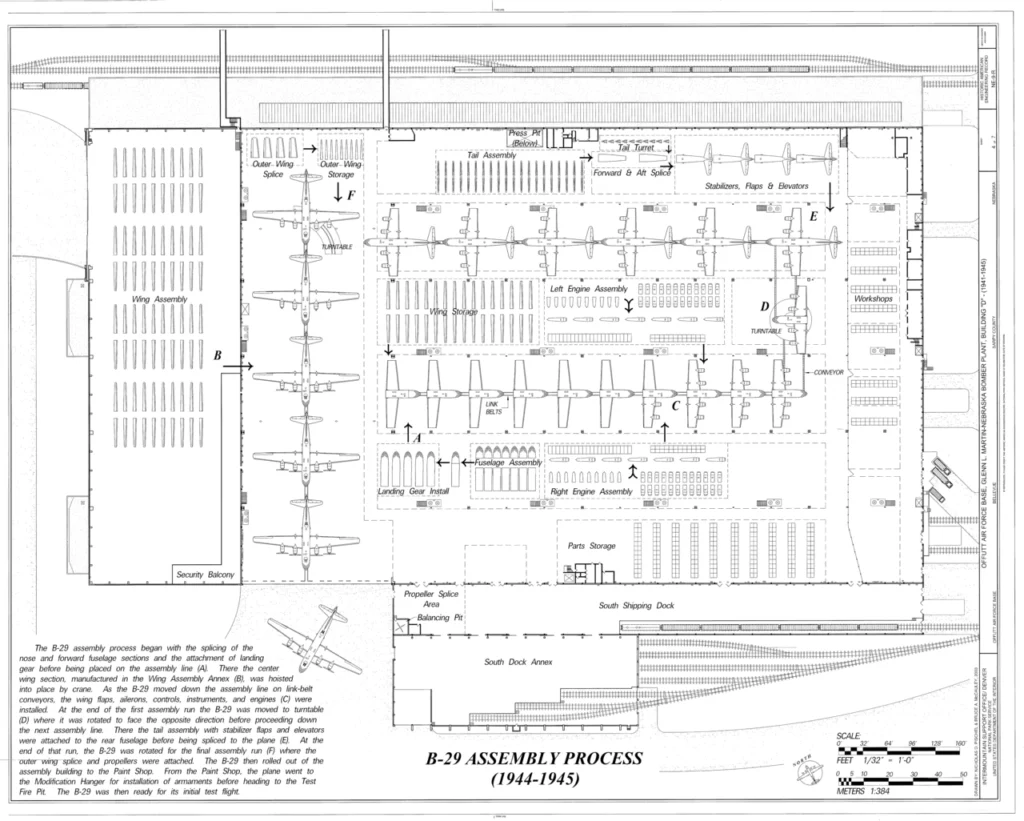
Initially, the B-29 production contracts were awarded to the Fisher Body Division of General Motors in Cleveland but were later transferred to the Martin Company. The first B-29 assembled by Martin was completed in June 1944, and the number of employees reached its peak of 14,500 by November 1943, with 40% being women.
The Martin Omaha facility functioned primarily as an assembly plant, with the center wing section being the most significant component manufactured on-site. Similarly to the Boeing-Renton facility, only the center wing sections were produced at Martin-Omaha, while the rest of the components were subcontracted.
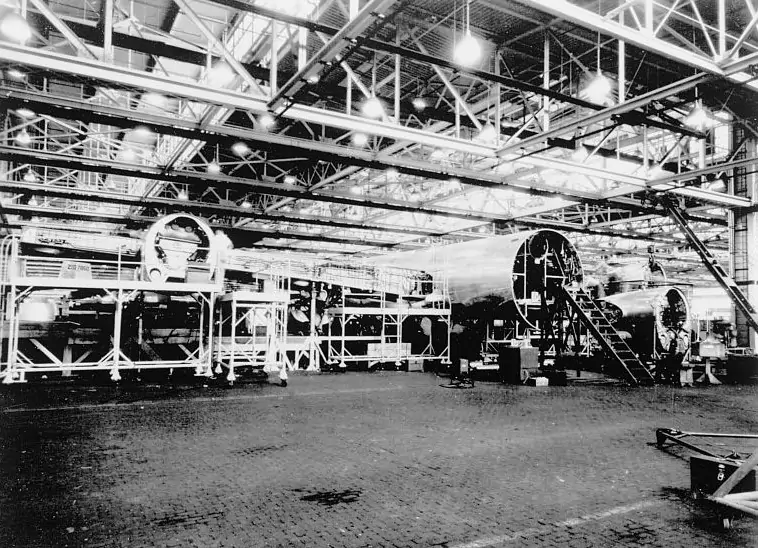
In early 1945, Martin-Omaha was capable of producing 55 bombers per month with fewer modifications compared to B-29s produced in other factories. The Air Force highly praised the plant’s quality control and it was awarded the Army-Navy “E” Award four times. It was also selected as the source for the Silverplate bombers, which were designed to carry atomic bombs.
At the end of the war, Martin-Omaha had constructed 536 high-quality B-29s.
Boeing-Seattle
In the early 1940s, the Boeing Aircraft Company embarked on a massive plant expansion program that saw the company’s Seattle Plant 2 undergo significant expansion. The plant, which was initially 15,422 square meters, was enlarged to 160,260 square meters, making it the company’s largest production plant and administrative headquarters.
The government played a key role in the expansion of the Seattle Plant 2, investing $17.5 million to build the facility for the production of the B-17 Flying Fortress.
In 1943, despite the remarkable feat of producing 3,600 B-17s and spare parts, the facility was tasked with converting its production lines from the B-17 to the B-29 Superfortress.
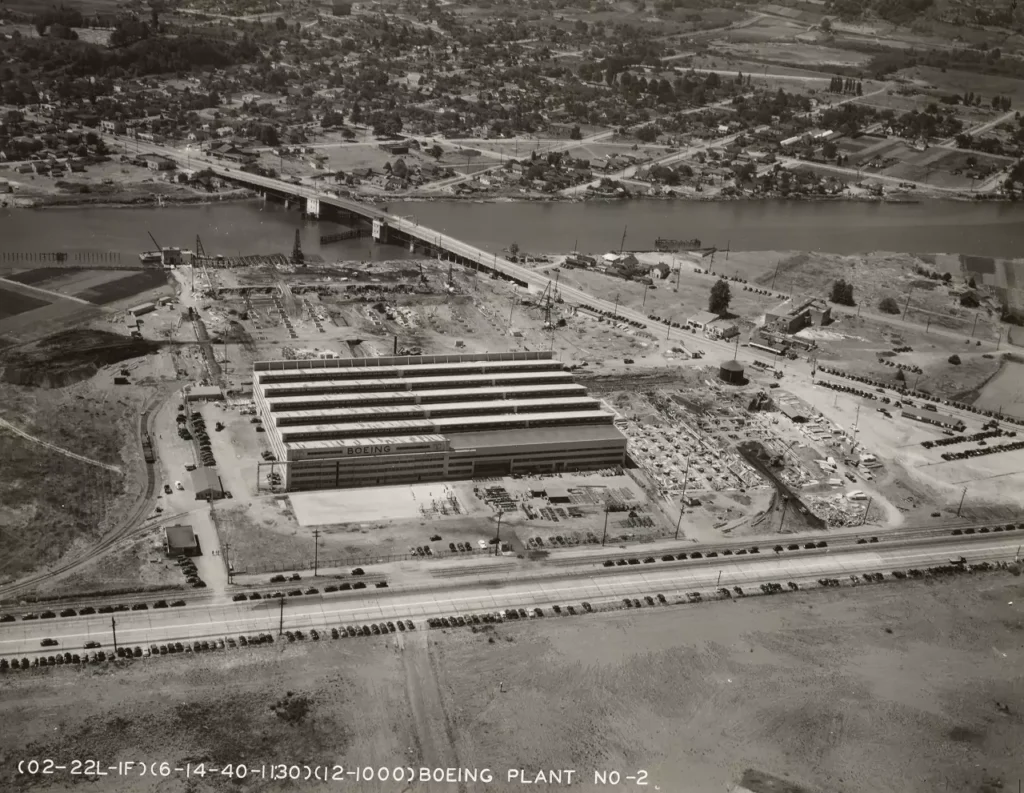
With the ongoing heavy production of the B-17, creating additional production lines for the B-29 seemed like an impossible feat, as the plant was not equipped with the necessary room to accommodate the change.
With limited space available, the B-17 production lines had to be gradually reduced, with the B-29 jigs eventually taking up residence in a portion of the B-17 factory.
The Seattle plant was responsible for producing subassemblies for the B-29, with the final assembly taking place at the Renton facility. The transport of these completed subassemblies posed a problem, with the existing route featuring a low overpass and the alternate route being inadequate. To solve this issue, a brand new four-lane highway was built linking Seattle to Renton, for $450,000.
Despite these obstacles, the Boeing Seattle Plant 2 facility was able to produce three XB-29-BO prototypes, which were fabricated in major sections at Seattle Plant 1 before being barged upstream to Plant 2 for final assembly and flight testing.
Boeing-Renton
The Boeing-Renton plant was established to produce large patrol aircraft for the Navy, designed to be launched from nearby bodies of water. The facility was expansive, measuring 1,100ft x 900ft with a total area of 1.7 million sqft, and came for $22.5 million, plus an additional $2.5 million for the surrounding land.
However, the Navy ultimately transferred ownership of the Renton plant to the Army Air Forces (AAF) in exchange for the AAF’s North American plant in Kansas City, which was used for the production of the B-25 bomber.
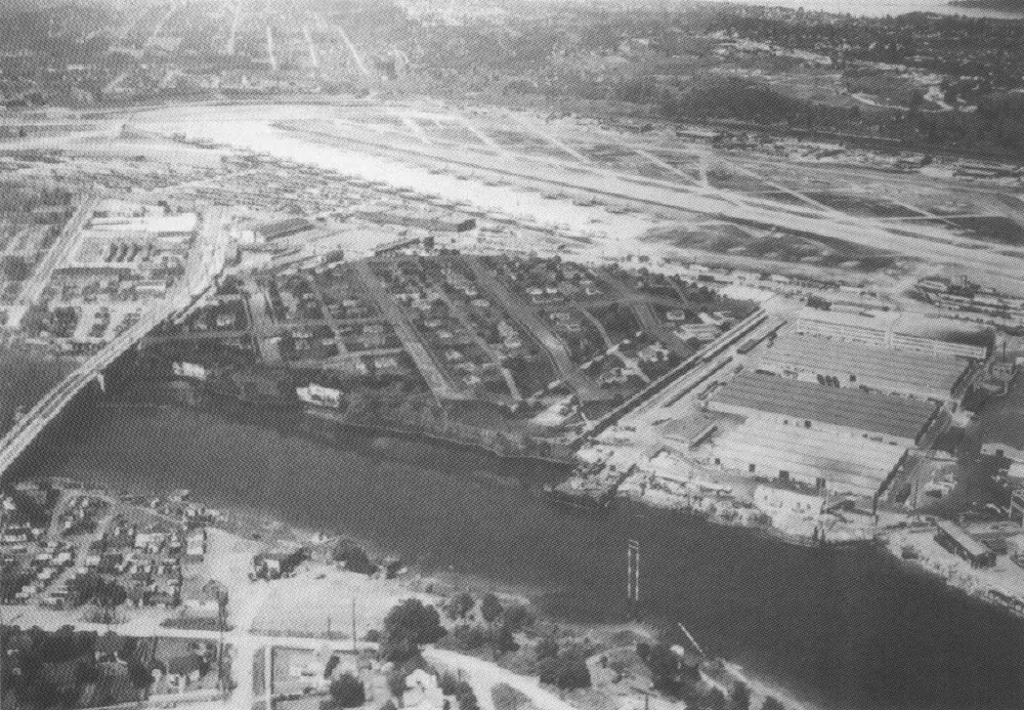
On December 21st, 1943, the Renton facility produced its first B-29A (42-93824) and it completed its maiden flight on December 30th of the same year. The plant encountered several challenges, including labor disputes, while also having to maintain production schedules and transferring much of its fabrication machinery and jigs to Seattle and its branch plants.
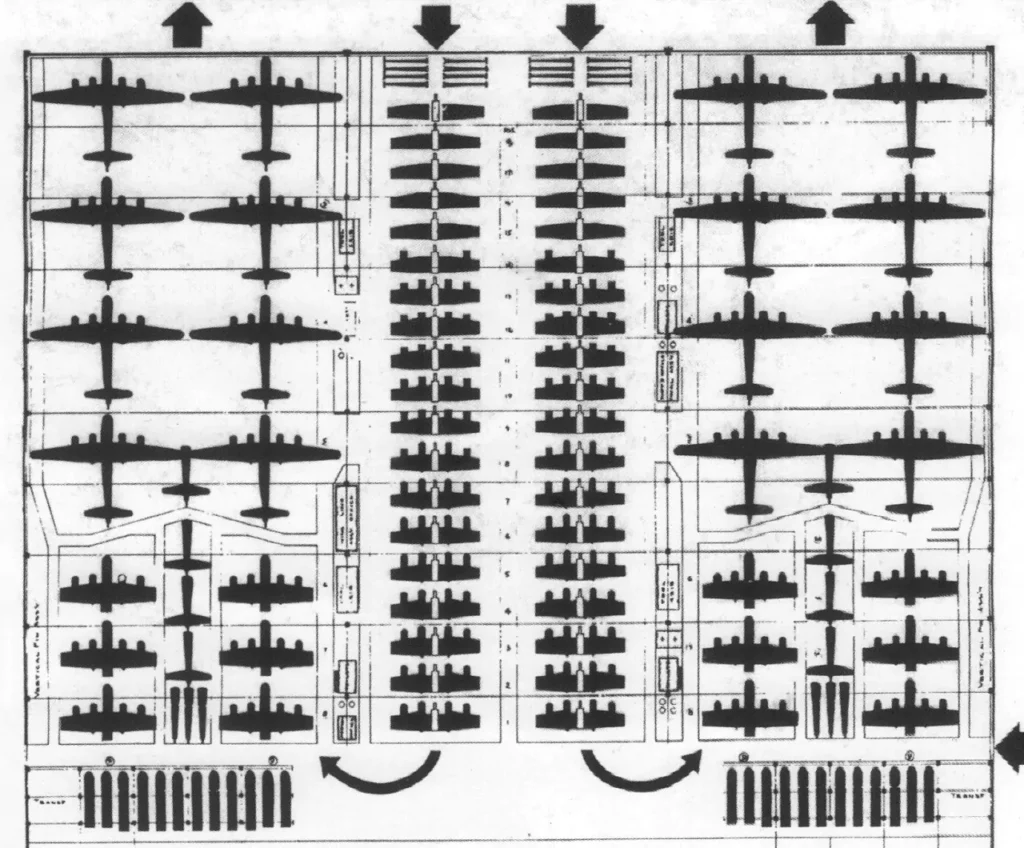
By August 1944, the Renton plant employed approximately 7,500 individuals, including 2,550 women and 2,010 men on the production line, with the rest mostly being women in administrative positions.
The facility was able to assemble 160 B-29 Superfortress bombers per month by July 1945, surpassing the output of any other B-29 factory. However, as the B-29s consisted of subcontracted components, they required more time to be spent at modification centers.
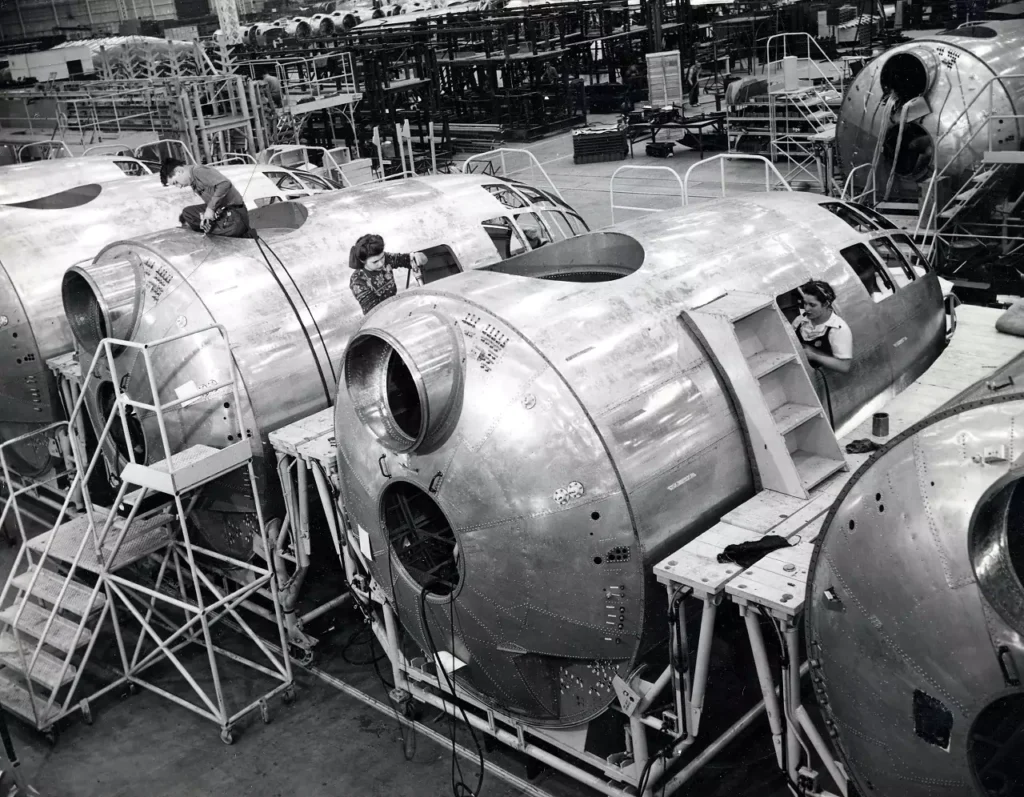
Throughout the war, Boeing’s Seattle and Renton facilities produced 1,119 B-29 Superfortress bombers. The Renton plant alone produced a total of 1,122 B-29A Superfortress bombers by the end of production. The final B-29A-75-BN (44-62328) was manufactured at the Renton facility on May 28th, 1946, and delivered to the United States Army Air Forces (USAAF) on June 10th, just 12 days later.
Subcontractors
In addition to the main four plants, subcontractors were needed to supply parts and components to the main contractors.
Notably, the project relied heavily on over 1,400 companies providing a diverse range of parts, totaling over 40,000 different components. Furthermore, the complexity of the aircraft was highlighted by the nose section alone, which required over 50,000 rivets and 8,000 different parts.
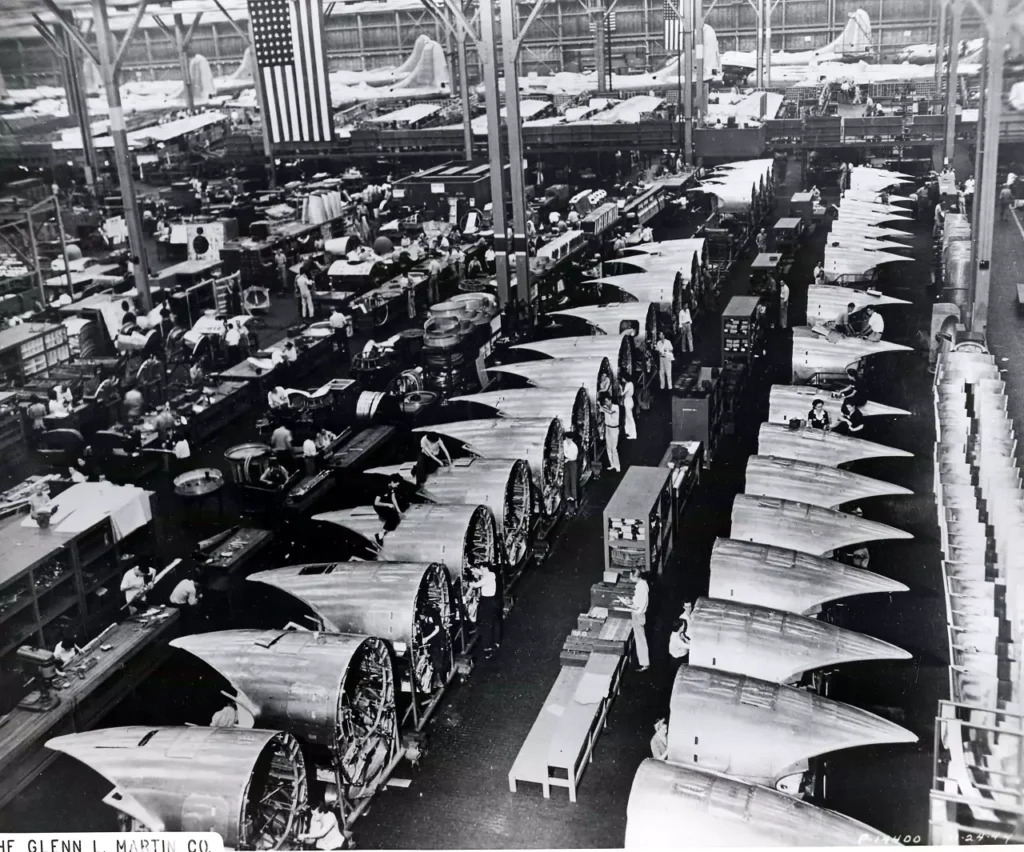
Additionally, the automobile industry played a vital role in the mobilization efforts for the B-29 project, with companies such as Chrysler and Hudson, despite their lack of prior experience in aircraft design, making significant contributions to the project’s success.
Some notable subcontractors of the nationwide effort:
- Hudson Motor Car Co. (Detroit, MI): Produced 802 B-29 rear fuselages, bulkheads, outer wing panels, and wingtips
- Fisher Body Division of GM (Cleveland, OH): Produced 13,772 B-29 engine nacelles, 566 nose sections, outer wing sections, and complete tail sections
- Dodge (Chrysler) (Chicago, IL): Produced Wright R-3350 engines for B-29s
- Frigidaire Division of GM (Dayton, OH): Produced all B-29 Hamilton Standard propellers
- Murray Corporation (Scranton, PA): Built 500,000-square-foot plant to build B-29 wings, wing edges
- Briggs Manufacturing Company (Detroit, MI): Supplied empennage, outboard wing, dorsal fins, and stabilizers to all B-29 assembly plants.
- DeSoto Division (Chrysler Corporation) (Warren, MI): Built the engine cowlings.
- Goodyear Aircraft (Akron, OH): Built the leading edges for the wing elevators.
For a more completed list of subcontractors check Building the B-29: The Subcontractor’s list
Productions blocks
During World War II, the US Army Air Forces (USAAF) implemented a system known as the Block Number System to keep track of the numerous modifications made to aircraft models. This system aimed to minimize the impact of these changes on manufacturers by grouping them together and introducing them at the start of a new production block.
Under the Block Number System, each aircraft model was assigned a letter, with changes indicated by consecutive numbers in blocks of five. The reason for this five-number skipping was to allow for field or factory modifications to be made to the designated dash-numbered model.
The B-29 aircraft was subject to this system as well. Despite attempts to limit the number of changes to the aircraft’s specifications, a significant number were still made. To address this, all planes within a given block (usually 50 or 100) were produced to the same agreed-upon specifications at the start of the block. This allowed manufacturers to maintain a consistent output of finished planes.
The production blocks for each aircraft type were typically incremented by 5 and included one of the following codes for the manufacturing plant:
- BO (Boeing-Seattle). The three XB-29s were built here.
- BN (Boeing-Renton). The N stands for Navy as it was initially to produce flying boats for the Navy.
- BW (Boeing-Wichita).
- MO (Martin-Omaha).
- BA (Bell-Atlanta). Located in Marietta, 20 miles west of Atlanta
However, it’s important to note that the block numbers of one manufacturer did not reflect the same changes in the same block number of another manufacturer.
Examples of this include Wichita B-29s reaching B-29-100-BW; Renton B-29s reaching B-29-75-BN; Bell-Marietta B-29s reaching B-29-65-BA; and Martin-Omaha B-29s reaching B-29-60-MO.
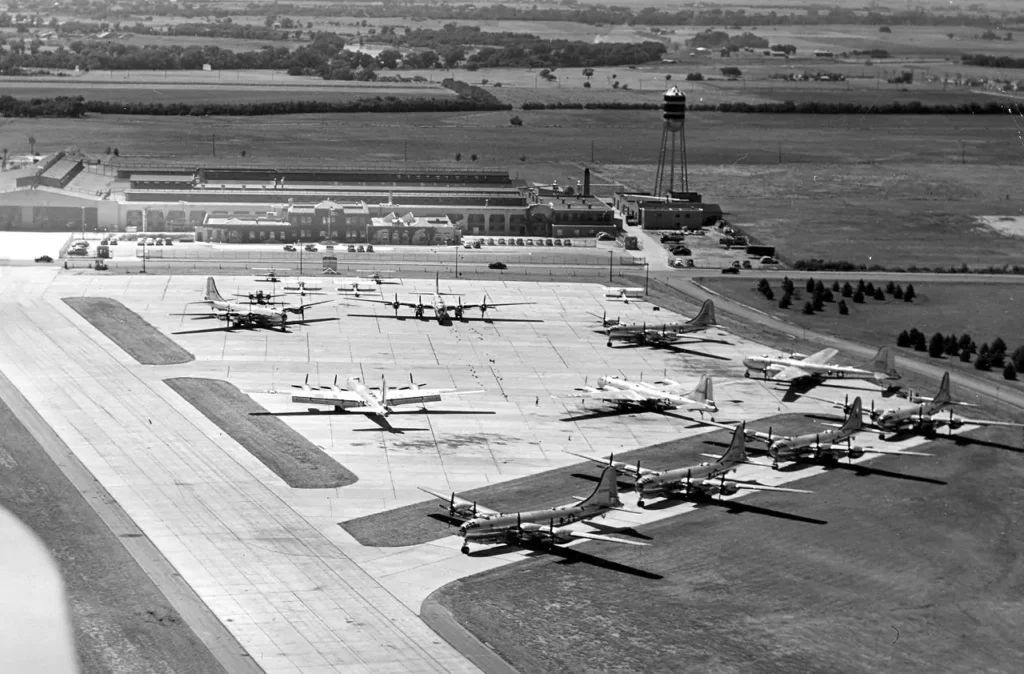
The B-29 production blocks saw a variety of modifications, with each manufacturer implementing the same change in different blocks:
- The R-3350-41 engine was utilized in the Boeing Block-50 design as well as the Martin and Bell Block-20s. Eventually, during the final stages of B-29 production, all three manufacturers adopted the R-3350-57 engine.
- The Boeing Block-40 models featured an increased armament in the forward top turret, with four .50 caliber machine guns. Similarly, the Bell Block-10s also included this feature. All Martin B-29 models had this armament from the start of production. On the other hand, the 20mm tail cannon was removed from the Boeing Block-55, as well as the Bell and Martin Block-25ss.
- Initially, the B-29s were designed to carry a fuel capacity of 8,168 gallons. However, later on, to increase this capacity, an additional four tanks were added to the center wing section. This brought the total fuel capacity to 9,438 gallons. Boeing made this modification on their Block-50 bombers, Bell on their Block-5s, and all Martin B-29s had these extra tanks as a standard feature from the start of production.
Production figures
Boeing B-29 Production by Model and Plant
Designation | Number | Location | Comment |
---|---|---|---|
XB-29-BO | 3 | Seattle, Washington | Prototypes |
YB-29-BW | 14 | Wichita, Kansas | Service test units |
B-29-1-BA | 5 | Atlanta, Georgia | Pilot ships |
B-29-1-MO | 5 | Omaha, Nebraska | Pilot ships |
B-29-BA | 357 | Atlanta, Georgia | |
B-29B-BA | 311 | Atlanta, Georgia | |
B-29-MO | 536 | Omaha, Nebraska | |
B-29A-BN | 1,119 | Renton, Washington | |
B-29-BW | 1,630 | Wichita, Kansas | |
Total | 3,980 |
Source: Boeing B-29 Superfortress (Crowood Aviation Series) by Steve Pace
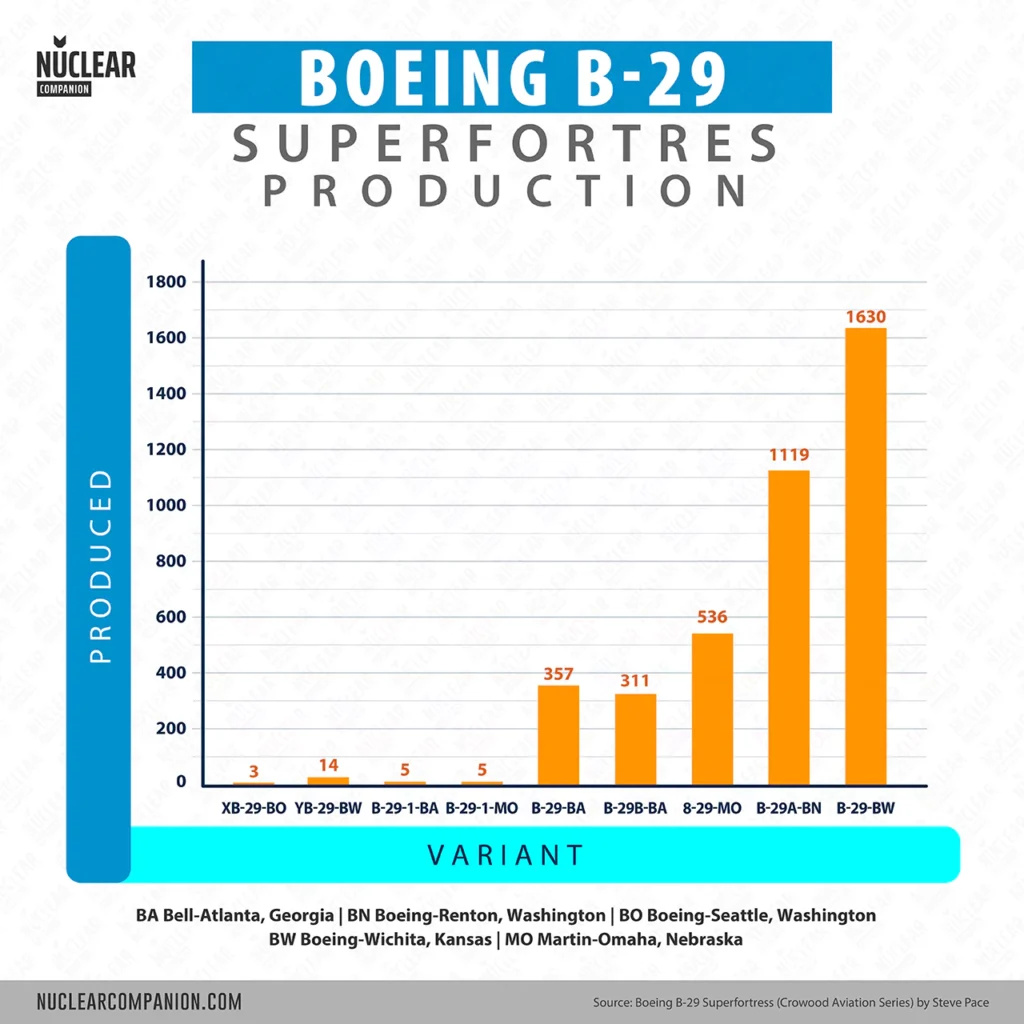
Boeing B-29 Monthly Production
1943 | 1944 | 1945 | |
---|---|---|---|
January | - | 54 | 221 |
February | - | 57 | 260 |
March | - | 60 | 291 |
April | - | 51 | 321 |
May | - | 88 | 350 |
June | - | 82 | 370 |
July | 7 | 75 | 375 |
August | 4 | 94 | 319 |
September | 15 | 122 | - |
October | 13 | 125 | - |
November | 18 | 163 | - |
December | 35 | 190 | - |
Source: Boeing B-29 Superfortress: The Ultimate Look: From Drawing Board to VJ-Day by William Wolf
Modification Centers
Upon being accepted into the U.S. Army Air Forces (USAAF) fleet, a B-29 underwent a modification process at specialized centers where the latest upgrades were implemented, bringing the planes up to the most current standards. Although it might have seemed less efficient, this two-stage updating method was effective in producing a vast number of aircraft.
The Bell factory stood out among the other three B-29 plants as it provided the AAF with an aircraft that was ready for combat. The other plants delivered their finished product to the following modification centers:
- U.S. Government Modification Center No. 8 in Omaha, Nebraska operated by The Glenn L. Martin Company. The facility occupied 87.3 acres and featured 9 buildings with a combined area of 747,689 sq. ft.
- U.S. Government Modification Center No. 13 in Denver, Colorado operated by Continental Airlines Inc. The center was situated next to the Denver Municipal Airport, covering an area of about 900 acres. It featured a large modification hangar with an area of about 400,000 sq. ft.
- U.S. Government Modification Center No. 14 in Birmingham, Alabama. It was built in 1943 and operated by the Bechtel-McCone Corp. It was one of the largest modification centers of the USAAF, with a main Modification building that had a floor area of 1,440,000 sq. ft. and employed 5,200 workers.
In October of 1944, 148 modifications were slated for the B-29s being manufactured at the four factories. The Boeing-Renton plant was slated for the most modifications, a total of 75, followed by 31 modifications at the Boeing-Wichita factory, with 19 modifications for the Bell models and 18 modifications for Martin Omaha versions.
At the height of production in December 1944, the cost of modifying a Renton B-29 in Birmingham was exorbitant, averaging 30,000 man-hours. However, by May of the following year, this figure had plummeted to less than 10,000 man-hours as the efficiency at the Renton plant improved dramatically.
Conclusion
Despite the success of designing and building the prototype, manufacturing the B-29 proved to be a difficult task due to its unprecedented size and cost.
As a result, the B-29 was the largest aeronautical project in history and the most complex airplane ever built. But, the American business, along with the Army, took on the challenge of producing and developing the B-29, forging a new working relationship that lasted beyond World War II.
Further reading
- Boeing B-29 Superfortress Facts: 11 things to know
- How much did the Boeing B-29 Superfortress cost?
- Building the B-29: The Subcontractor’s list
- Building the B-29: The contracts List
- Building the B-29: Designations and Serial Numbers
Bibliography
- Boeing B-29 Superfortress (Crowood Aviation Series) by Steve Pace
- B-29 Superfortress in detail & scale, Part 1: Production Version – D&S Vol. 10 by Alwyn T. Lloyd
- Boeing B-29 Superfortress: The Ultimate Look: From Drawing Board to VJ-Day by William Wolf
- The Plant Finder: An Inventory of Government-owned Industrial Plants, September 1946
- Freedom’s Forge: How American Business Produced Victory in World War II, by Herman, Arthur
Who developed the entire production line at Hotel Del Coronado during one very long weekend.
The production line at Hotel Del Coronado wasn’t developed during a single weekend, nor by one person. The hotel, known as The Del, was built in 1888 and was considered technologically advanced for its time. It was not a production line in the modern sense, but rather a process of construction and staffing that took time and effort.
The story of The Del’s construction is more about the vision and investment of its developers, Elisha Babcock Jr. and Hampton L. Story, rather than a single “production line” developed in a weekend. They bought the land and oversaw the construction of the hotel, which was a significant undertaking for the time.
The production line at Hotel Del Coronado wasn’t developed during a single weekend, nor by one person. The hotel, known as The Del, was built in 1888 and was considered technologically advanced for its time. It was not a production line in the modern sense, but rather a process of construction and staffing that took time and effort.
The story of The Del’s construction is more about the vision and investment of its developers, Elisha Babcock Jr. and Hampton L. Story, rather than a single “production line” developed in a weekend. They bought the land and oversaw the construction of the hotel, which was a significant undertaking for the time.